TOH’s Innovation Framework Improves Care Quality and Patient Experience
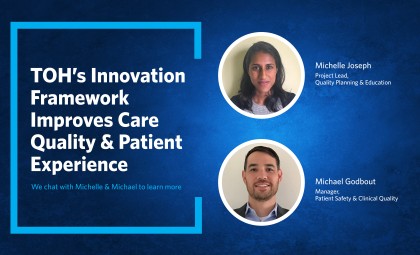
At this year’s Ottawa Patient Safety Conference, put on by The Ottawa Hospital (TOH), we had the opportunity to connect with the TOH team who support safety and innovation at the organization.
In addition to hearing about current projects on the go, we also learned how the culture of innovation is embedded across the organization and offers up an opportunity for anyone to drive change.
We sat down with Michelle Joseph, Project Lead, Quality Planning & Education, and Michael Godbout, Manager, Patient Safety & Clinical Quality, so we can share their story, with the goal of others in the sector scaling their learnings.
Why was this innovation framework created—what problem was the team trying to solve in creating it?
In 2015, TOH faced an internal dilemma. We knew we wanted to adopt a common methodology to guide quality improvement projects, but we had to decide which of the leading frameworks to use. We analyzed the four most commonly used frameworks (IHI’s Model, Six Sigma’s DMAIC, Comprehensive Unit-Based Safety Program (CUSP), and Lean management) and quickly realized there were pros and cons to each but not one single approach appropriate for the complexities and wide range of problems we face in healthcare.
We wanted to avoid confusion caused by having too many different philosophies, terminology, and tools and instead create one simple approach and common language for everyone undertaking a quality improvement (QI) project, so we created the TOH Innovation Framework.

Who was involved in creating this resource?
The TOH Innovation Framework was created under the direction of Samantha Hamilton, the director of the department of Quality and Patient Safety. Her team of Process Engineers and QI Coordinators drew upon their formal training in QI, project management and biomedical engineering, as well as their experience working in healthcare at organizations such as the National Health Service (UK) to create this novel framework.

What types of projects is it used for?
The beauty of the TOH Innovation Framework is that it is simple enough to be used for a small QI project led by someone doing QI for the first time, but it also provides the rigour for large scale system redesign and transformation work.
How did you spread the word about the framework?
Internally we offer several courses including our popular Intro to QI course. To date, over 1400 staff, physicians, and residents have completed the training. The framework is also taught externally in the Telfer Executive Programs Quality Improvement and Patient Safety Leadership Program through the University of Ottawa and CHA Learning’s Health Quality Innovation Program.
It was also published in the International Journal for Quality in Health Care in 2020. Use of the TOH Innovation Framework has spread very naturally and has most recently been adopted by the Royal College of Physicians and Surgeons of Canada as well as other hospitals in Ontario.
What’s the uptake been like?
There is no shortage of enthusiasm from staff and physicians across TOH who want to start a project of their own and who want to participate in our QI educational offerings. Our internal project registry currently contains over 600 QI projects.
Can you share an example of a project or initiative that used the framework and the outcomes?
There are so many that it’s hard to choose, but a recent success story is from the Outpatient Blood Lab at TOH. Faced with unacceptably high wait times for outpatient lab services, poor patient experience, and wasted resources, a QI project was undertaken.
Data was analyzed to assess the extent of the problem and a clear objective and targets for improvement were established. From there, the process was mapped out, problems were identified, and a new process was designed to increase efficiency. After just a short amount of time, the average wait time was reduced by 72 per cent and patients were ecstatic about the new and improved experience.
What’s next for the team?
We are constantly looking for ways to make QI accessible to everyone at TOH. Over the last year, we have focused on creating micro courses—bite-sized education that focuses on a specific topic or tool. These courses can be consumed in live sessions or asynchronously, allowing users to watch them when they need them the most.
Thank you, Michelle and Michael, for this snapshot of how collaboration and innovation are driving change forward—congrats to you and the entire team at TOH!
Has your organization undertaken an innovation initiative that’s supporting a culture of safety? Let us know! We’d love to share your story. Reach out to us at [email protected].